Let's Get Started!
Please feel free to contact us. We will get back to you within 1-2 business days. Or just call us now.
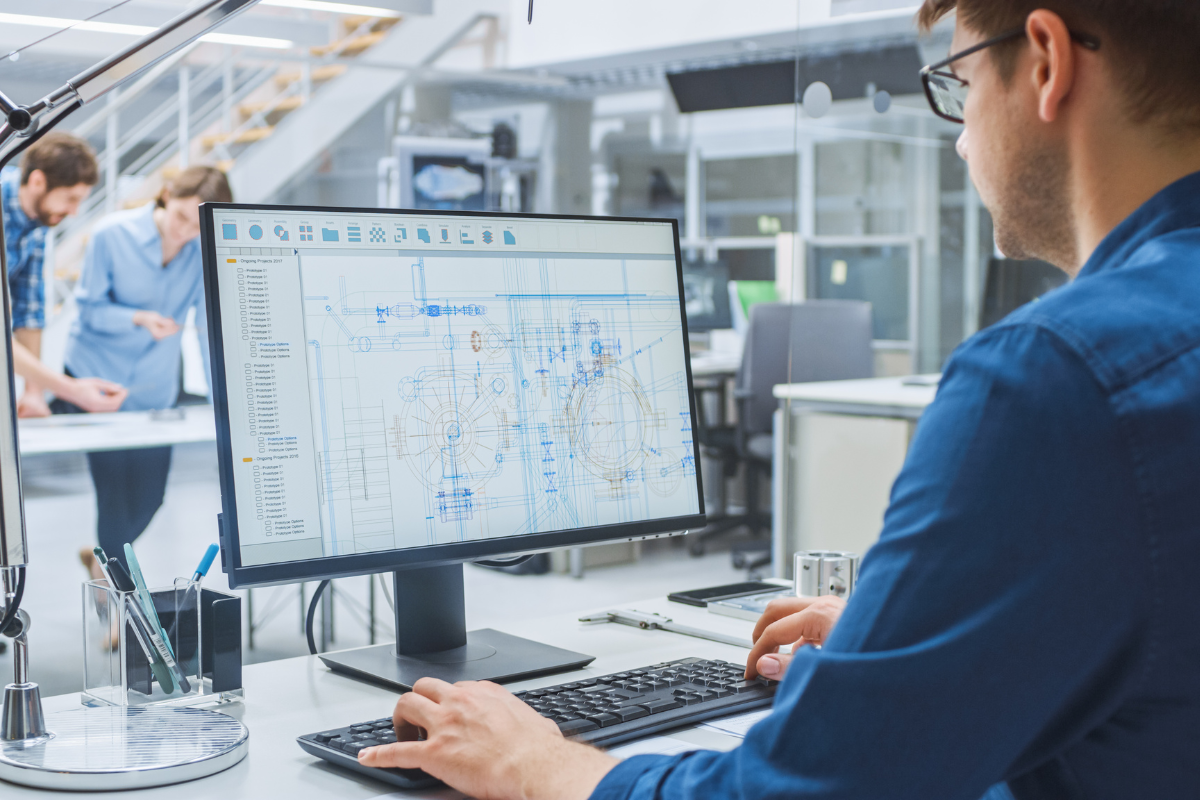
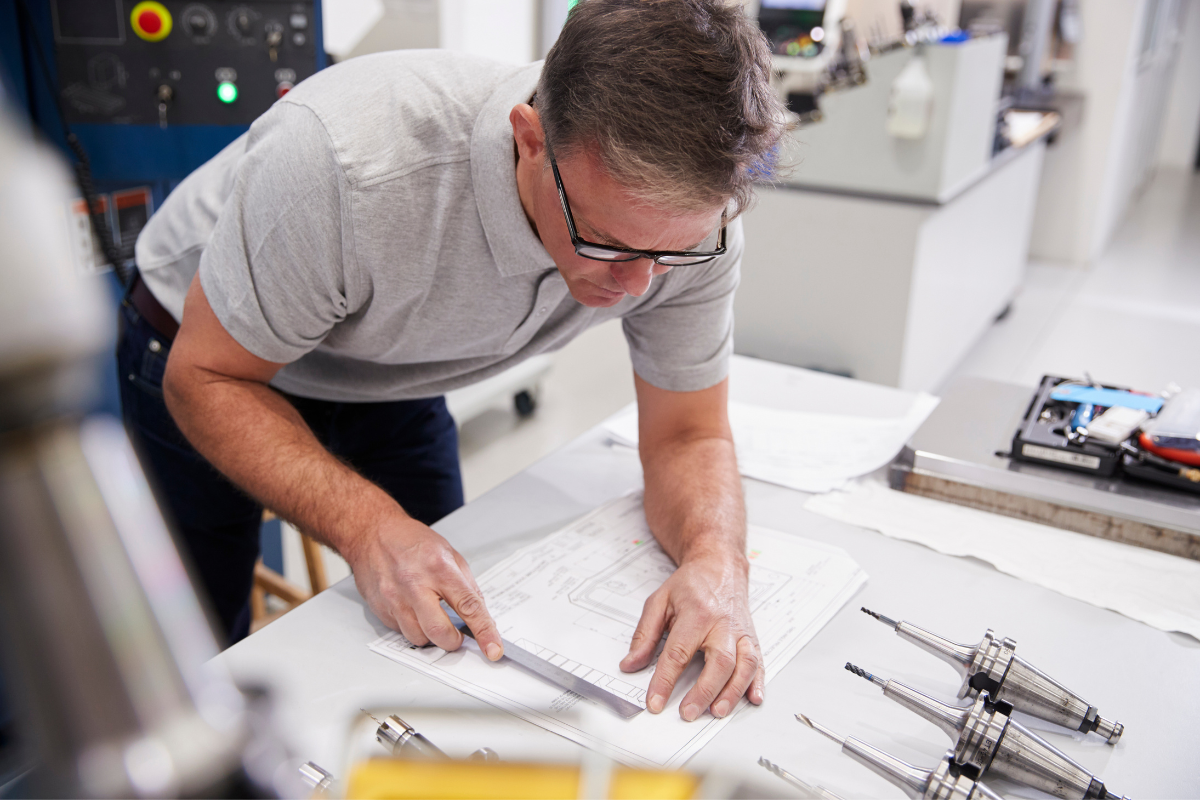
How can we help?
Through consultation, we invest the time to understand our customers’ needs in how their product is to be used, the lifespan and how it should look. With five approaches to tool building, we offer a wide spectrum of options that match the needs of the program, no matter where you are in your product lifecycle. Our strategy offers flexibility to start with a prototype tool design and as the development progresses modify the same tool for production, saving our customers thousands of dollars.
A successful program begins with a well-designed mold. We offer one of the most robust Design for Manufacturing analysis in today’s market that addresses all aspects of the parts design, performance and aesthetics. Our team of engineers and journeyman will ensure the sustainability and repeatability of your product.
What we offer:
- Offer Comprehensive Product Development Services: Engineering, Design for Manufacturability (DFM), In-house tool build, Texturing Division, and Tool Transfer programs
- Provide Wide Range Tooling Capacity: 60 tons to 2,000 tons
- Work with the latest CAD technology and software
- Have over 50 years of experience designing and building molds
Our Solutions & Benefits
Our skilled engineers turn concepts into precise blueprints and provide ongoing support throughout production. Our engineering services deliver:
- Precision & Accuracy: We employ the latest technology and best practices to create detailed, accurate tool designs.
- Risk Mitigation: Our engineers identify and mitigate potential issues before they become costly problems.
- Collaboration: Our team of engineers are readily available to consult on design or material questions.
Design for Manufacturing (DFM). Designing a product for manufacturability and reliability is crucial for cost-effective production. Our DFM services offer:
- Assured Quality: We ensure that your design is manufacturable, minimizing defects and enhancing product quality.
- Cost Reduction: By addressing manufacturability obstacles early in the design phase, we save you time and money in the long run.
- Comprehensive: Our DFM analysis considers over 40 points of the mold design while adhering to the part’s unique specification to align prior to development.
A key core competency for General Pattern provides control and experience over the entire program life from prototype, preproduction to production needs:
- Competitive: In-house capabilities support shorter lead-times and competitive pricing on your investment.
- Turnkey: We will match the right tool design with the program to produce a few parts to a few hundred thousand.
- Reliable: Our team of journeyman offers the ability to turn and debug tool changes quickly and effectively to maintain tooling over the program life.
No matter the reason for transferring an existing tool, you can trust GPC to develop a plan and execute to make the transition seamless.
- Peace of Mind: Ability to inspect and recommend repairs through our tooling division with unprecedented speeds.
- Checklist: At the forefront, each tool is evaluated in our tooling department prior to set up.
- Faster Time-to-Market: Streamlined processes result in faster production times, giving our customers a competitive edge.
Technology Overview
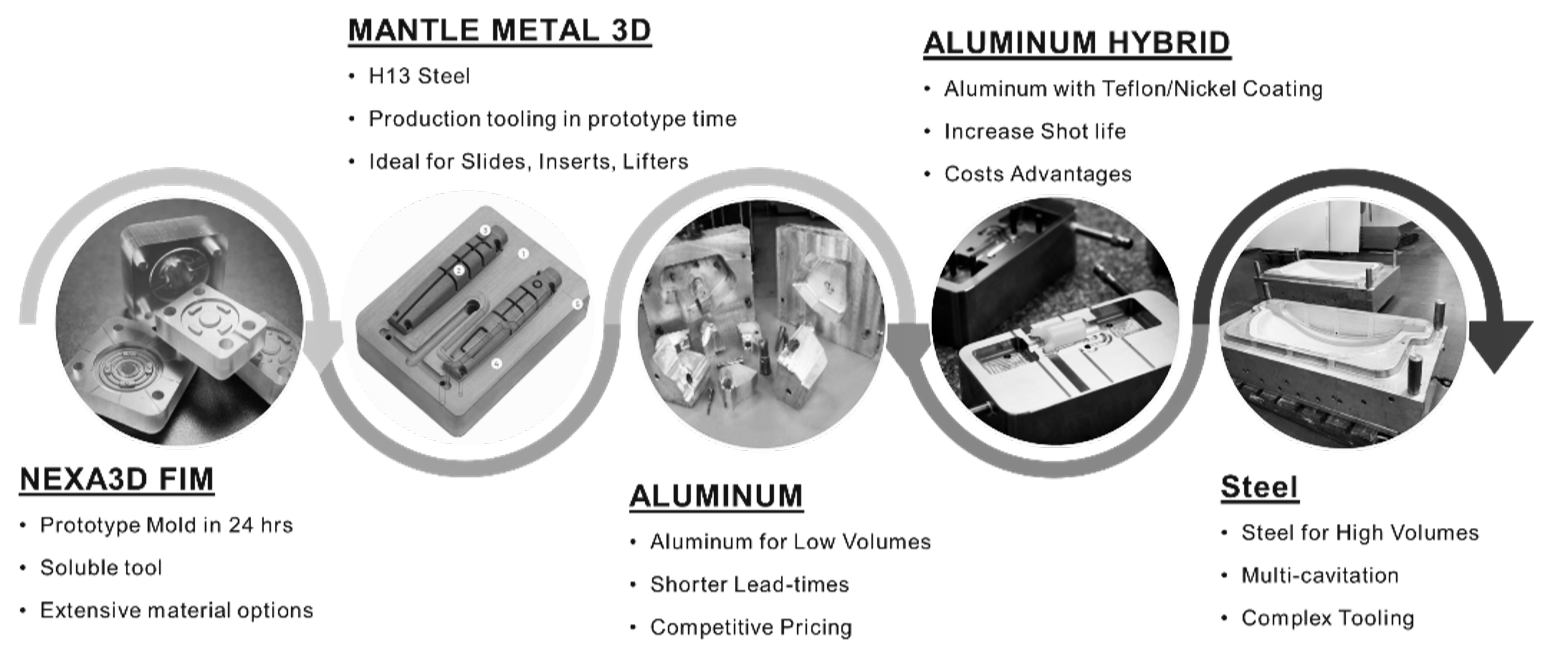
FAQs
With a design concept in mind, we can work together to refine and optimize your product. Our team can assess your concept for manufacturability, cost-effectiveness, and sustainability, making sure your design aligns with industry standards and regulations.
DFM services offer several benefits, including improved product quality, cost reduction, and faster time-to-market. By identifying and minimizing manufacturing challenges early in the design phase, we can save you time and money while ensuring a smoother production process.
Yes, we offer prototyping services as part of our product development process. Prototyping allows you to test and refine your product design before committing to full-scale manufacturing, reducing the risk of costly errors and ensuring a high-quality final product.