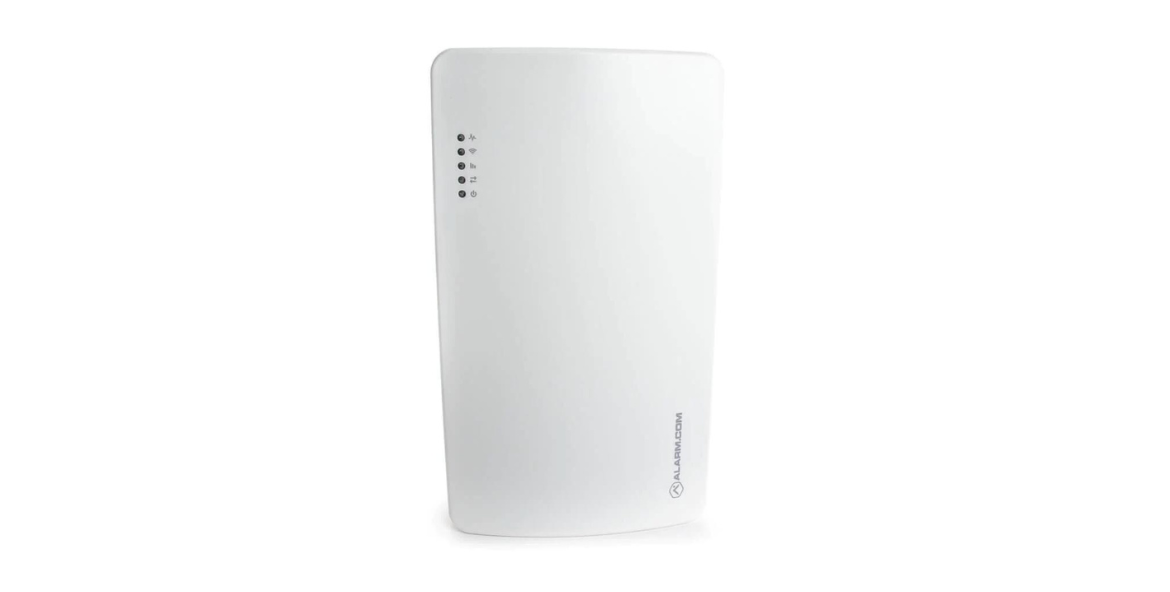
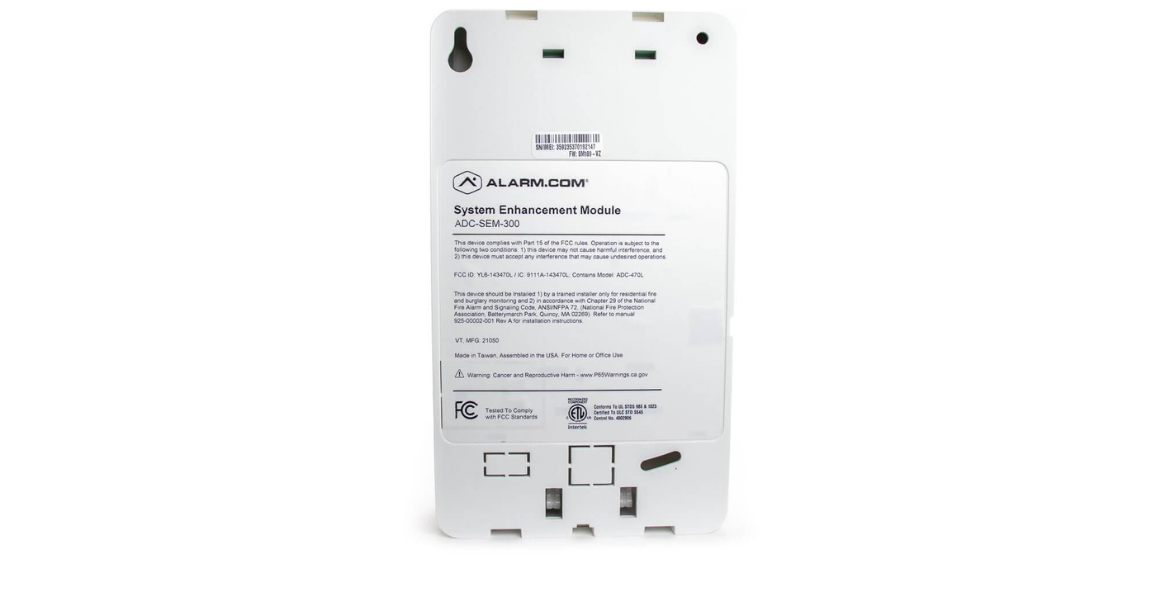
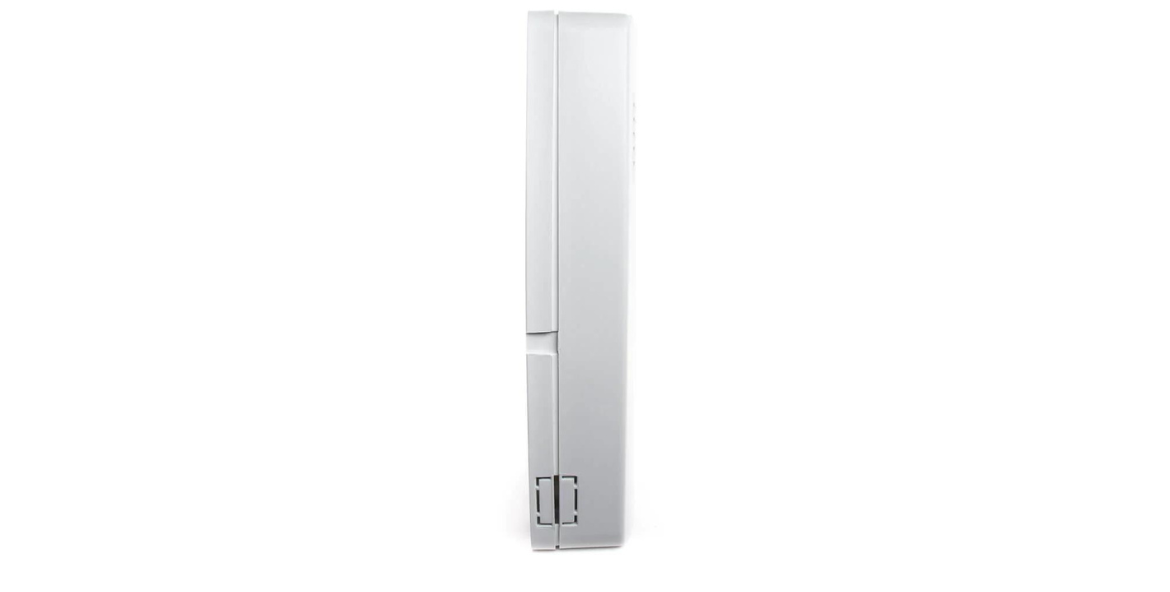
Let’s Work
Together!
Please feel free to contact us. We will get back to you with 1-2 business days. Or just call us now.
Process & Technologies
3D Printing & Check Model: Initial prototypes were developed using state-of-the-art 3D printing technology, ensuring precision and adherence to design specifications.
High Volume P20 Steel Tooling: Utilizing P20 steel tooling, known for its durability and strength, enabled us to achieve high-volume production without compromising quality.
Work Cell Development for “At the Press” Operations: Our innovative work cell development for at-the-press operations streamlined the production process, enhancing efficiency and consistency.
Second Operations: We implemented meticulous secondary operations, ensuring each component meets our stringent quality standards.
Heat Staking Lightpipe: This specialized process was used for integrating lightpipes, essential for electronic housing functionality and aesthetics.
2-Color Pad Printing: Advanced 2-color pad printing techniques were employed to add detailed, durable graphics to the housing components.
Kitting: Each component was carefully kitted, ensuring seamless assembly and integration for our clients.
Materials
- PCL ABS: Selected for its strength and flexibility, PCL ABS is ideal for demanding electronic housing applications.
- Polycarbonate: Known for its durability and resistance to impact, polycarbonate was used to enhance the longevity and reliability of the product.
Delivery Timeline
- 6 Weeks: Demonstrating our commitment to efficiency, the entire project from conception to delivery was completed in a remarkable 6-week timeframe.
Unique Attributes
- Combination of CNC & 3D Printed Metal Technologies: A highlight of this project is the innovative use of both CNC and 3D printed metal technologies. This approach enabled the development of a multi-cavity tool, capable of supporting in excess of 1 million cycles.
- Self-Contained Semi-Automated Tray Assembly: We engineered a self-contained, semi-automated tray that assembled and decorated the parts within the injection architecture. This system not only increased production efficiency but also ensured high precision and consistency across all components.
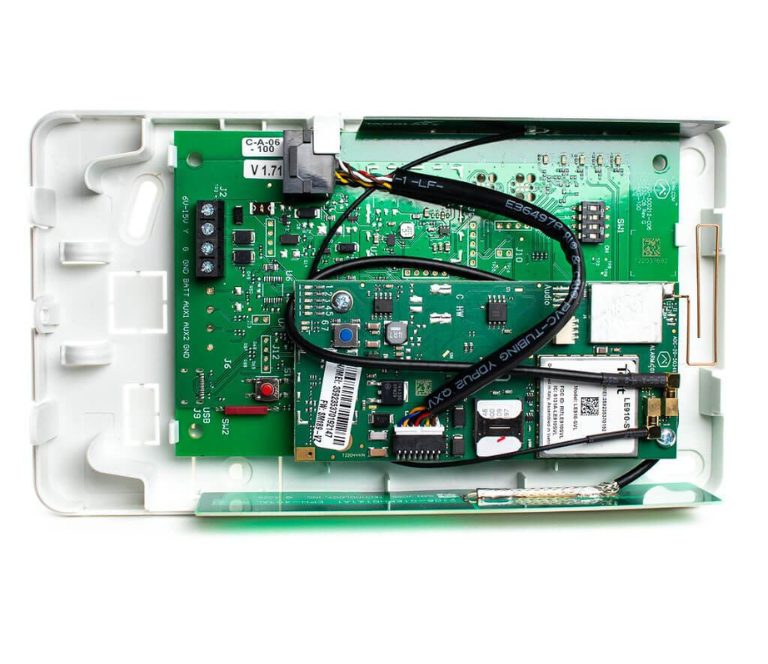
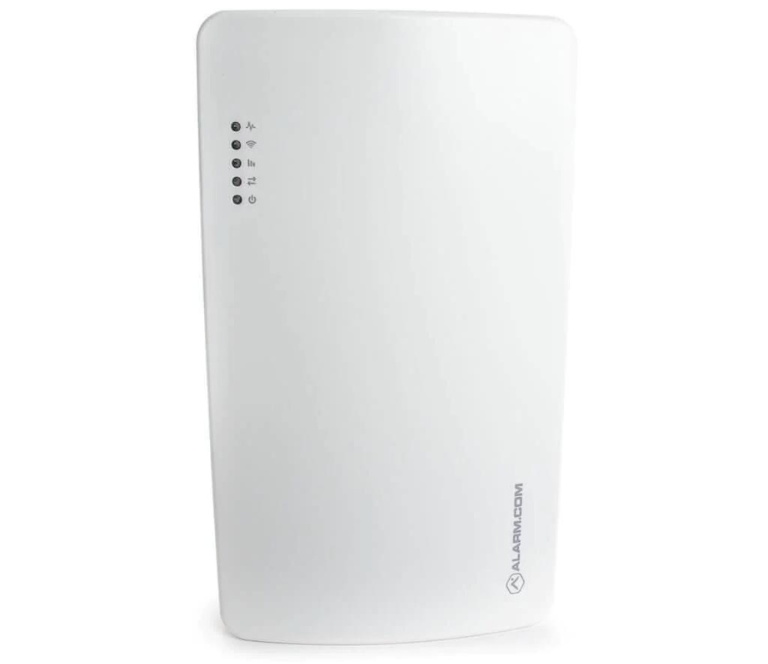
Conclusion
This project by General Pattern Company exemplifies our ability to blend traditional and modern manufacturing techniques to deliver high-quality, efficient solutions for Alarm System Store in the consumer electronics industry. Our commitment to innovation, precision, and speed positions us at the forefront of electronic component manufacturing.