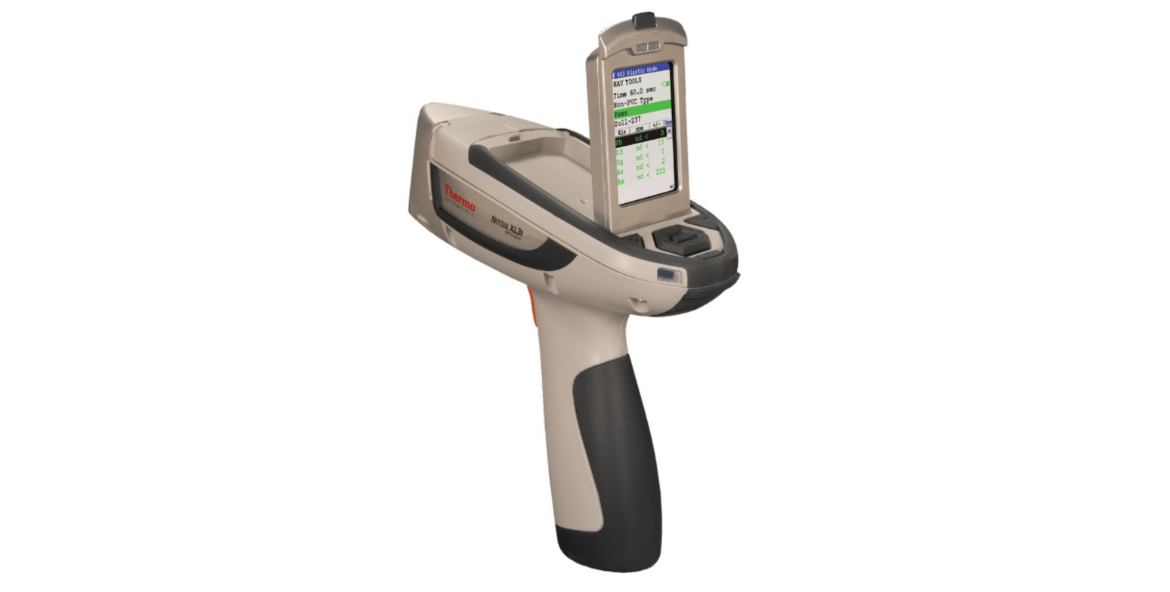
Let’s Work
Together!
Please feel free to contact us. We will get back to you with 1-2 business days. Or just call us now.
Process & Technologies
Bridge Production: To meet immediate needs, GPC utilized bridge production methods, which allowed for the transition between prototype and full-scale production with agility and precision.
Rapid Tooling: GPC employed rapid tooling strategies to quickly produce molds for injection molding, significantly cutting down development time while maintaining high-quality standards.
Injection Molding: The injection molding process was streamlined to handle the production of complex components efficiently, ensuring the analyzer parts were durable and met the exacting requirements of medical devices.
Materials
- Valox 325: A high-performance polyester known for its excellent chemical resistance, stiffness, and stability, Valox 325 was chosen for the structural components of the analyzer.
- Santoprene 201-50: For parts necessitating flexibility and durability, Santoprene 201-50, a versatile thermoplastic elastomer, was used to provide the necessary resilience and touch-friendly feel.
Delivery Timeline
2 Weeks for Trade Show: In an industry-leading turnaround, GPC delivered prototypes ready for a trade show within two weeks.
100 Sets of Components in 4 Weeks: Following the trade show, GPC continued to exceed timeline expectations by completing 100 sets of the analyzer components within an additional four weeks.
Unique Attributes
Capacity for Rapid Delivery: GPC was uniquely equipped with 13 stereolithography (SL) and 4 selective laser sintering (SLS) machines, making it the only company capable of meeting the demanding two-week delivery schedule.
Proprietary Polyurethane Molding Technique: Leveraging our proprietary production representative polyurethane molding technique, we could deliver units with molded-in color and texture. This approach meant that the prototypes not only resembled but also felt and functioned like the final production components.
Conclusion
The Niton Portable XL3t Analyzer project is a testament to General Pattern Company’s capabilities in rapid prototyping and production for the medical industry. By combining advanced technology with proprietary techniques and efficient project management, GPC delivered prototypes that met the critical needs of a trade show presentation and a continuing order. The success of this project reflects our commitment to innovation, quality, and speed, reinforcing GPC’s role as a pivotal partner in the medical device manufacturing landscape.