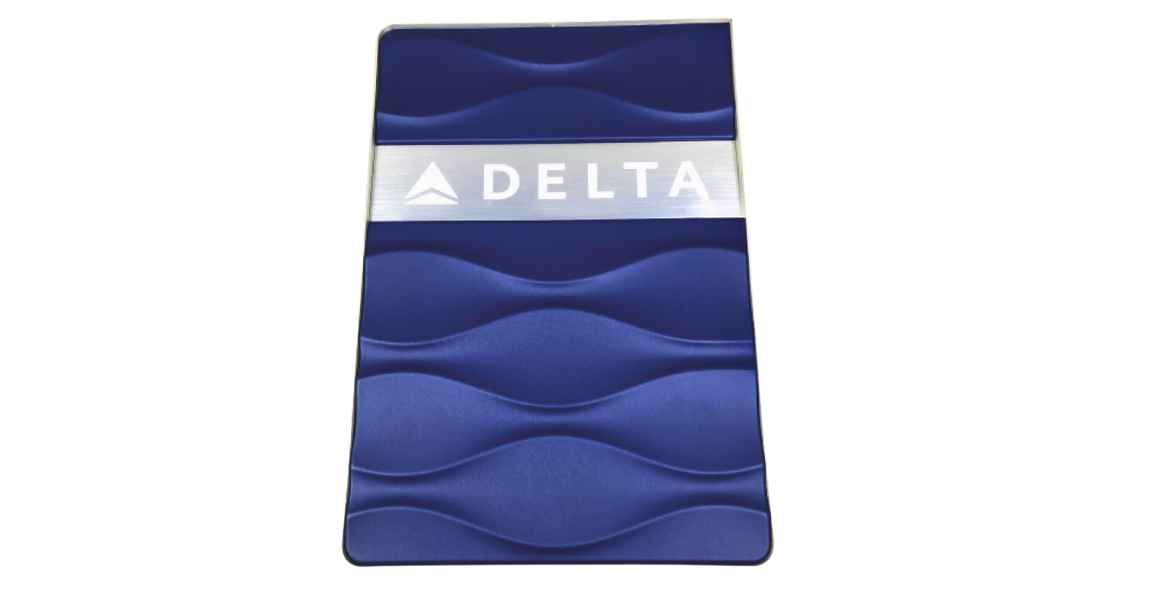
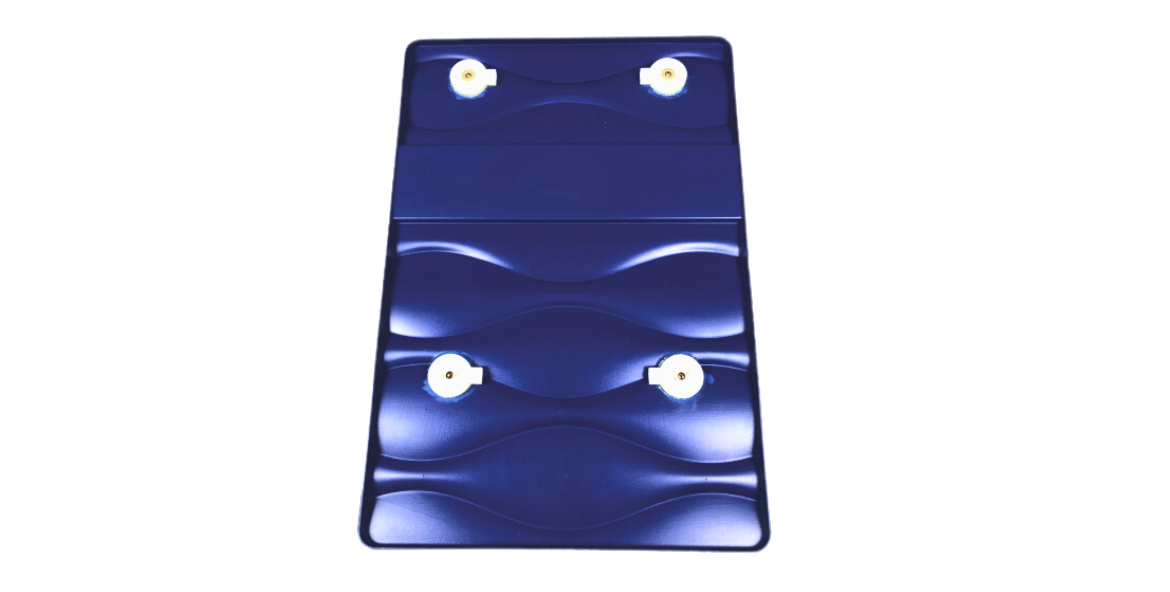
Let’s Work
Together!
Please feel free to contact us. We will get back to you with 1-2 business days. Or call us now.
Process & Technologies
- CNC Milling 3 & 5 Axis: Utilizing advanced CNC milling techniques with both 3 and 5 axis capabilities, GPC achieved intricate designs and precise specifications required for aerospace components.
- Vacuum Forming: Employing vacuum forming allowed for the creation of complex shapes and lightweight parts, crucial for aerospace applications.
- Low Volume Injection Molding: Specialized in low volume production, GPC provided customized, high-quality injection molded parts that meet the stringent standards of the aerospace industry.
- Metal Forming & Finishing: With our metal forming and finishing capabilities, we delivered components that not only fit perfectly but also met the aesthetic requirements of cabin interiors.
- Powder Coating: The application of powder coating ensured a durable and high-quality finish, resistant to the wear and tear of frequent aerospace use.
- Laser Scanning: Laser scanning technology was used for precise measurement and quality control, ensuring each component fit seamlessly within the cabin’s interior layout.
- Assembly: GPC’s skilled technicians meticulously assembled the decorative panels, integrating them flawlessly with existing cabin structures.
Materials
- Kydex: Chosen for its excellent formability, durability, and aesthetic qualities, Kydex was used primarily for the paneling surfaces.
- Aluminum: Utilized for its strength-to-weight ratio, aluminum components were integrated into the design for structural support.
- Delrin: Known for its low friction and high wear resistance, Delrin was used in components that required precision mechanical action.
Delivery Timeline
3 Weeks: Demonstrating GPC’s exceptional efficiency and dedication, the entire project from conception to delivery was accomplished in an impressive 3-week timeframe.
Unique Attributes
In-House Manufacturing and Assembly: A key factor to the project’s success was GPC’s capability to fully manufacture and assemble components in-house. This approach not only streamlined the production process but also allowed for stringent quality control and rapid turnaround.
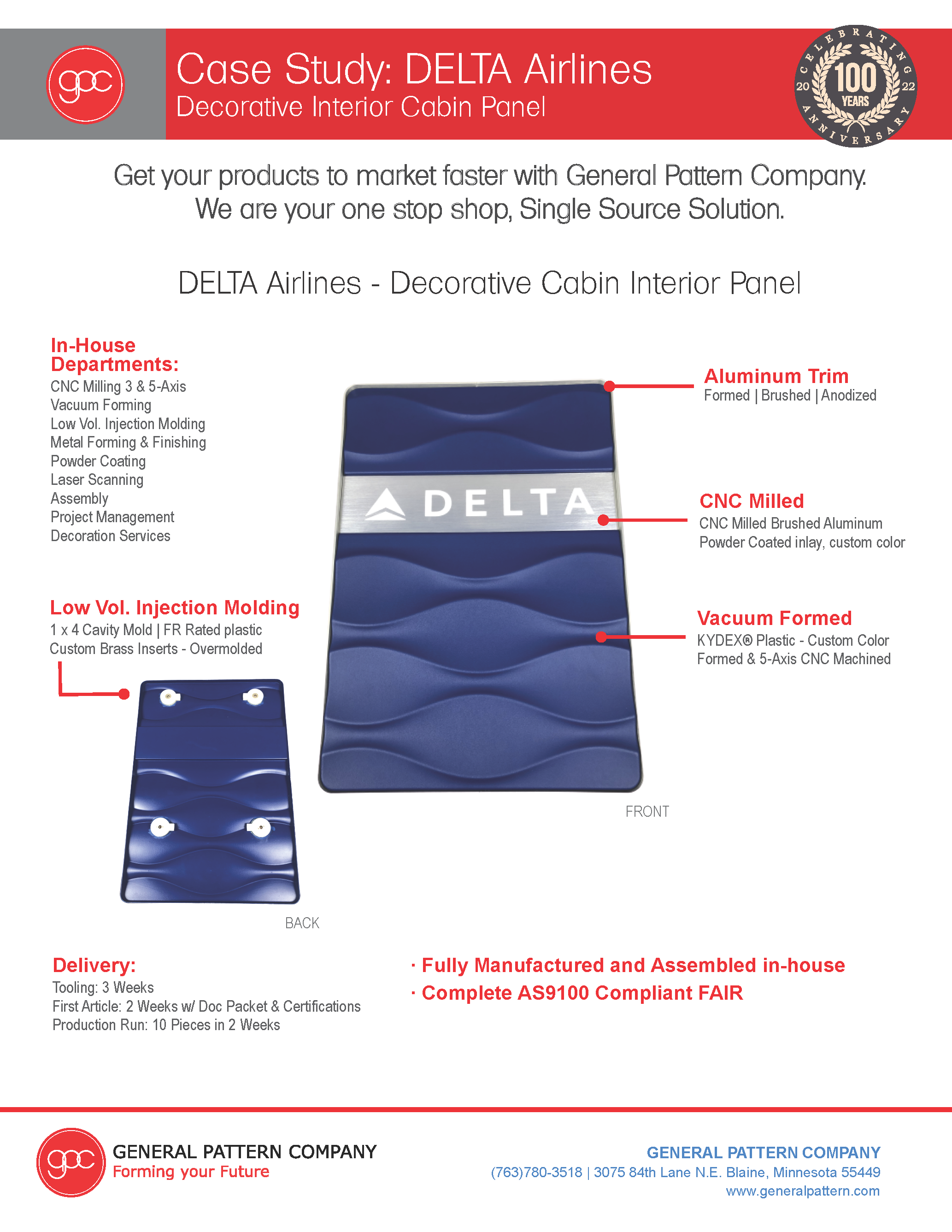
Conclusion
This project exemplifies General Pattern Company’s ability to address the unique needs of the aerospace industry through innovative manufacturing and assembly processes. By leveraging state-of-the-art technologies and our in-house capabilities, GPC delivered a high-quality, aesthetically pleasing decorative cabin interior panel within an unprecedented 3-week period. This achievement not only showcases our expertise and efficiency but also reinforces our position as a trusted partner in the aerospace sector, capable of delivering complex projects on an accelerated timeline.