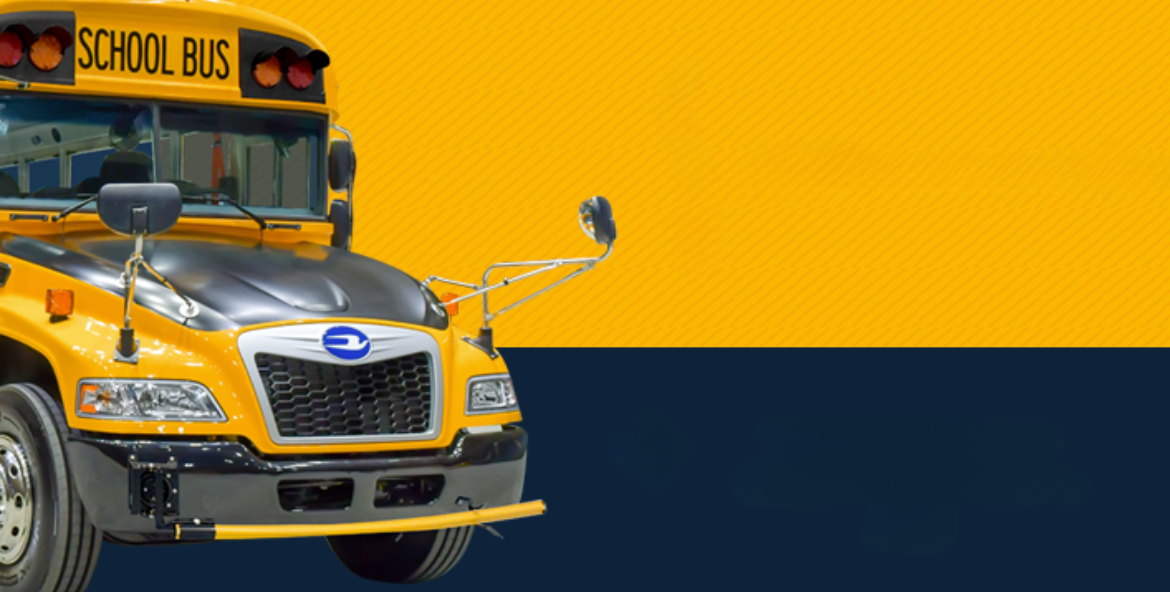
Let’s Work
Together!
Please feel free to contact us. We will get back to you with 1-2 business days. Or call us now.
Process & Technologies
- CNC Machined Prototype: GPC initiated the project with the creation of a high-precision CNC machined prototype, ensuring the design met all specifications and quality requirements.
- Low Volume Injection Mold Tooling: Leveraging GPC’s proprietary “speedway” technology, we developed specialized low volume injection mold tooling, tailored to efficiently produce the 2-piece grill.
- 1200 Ton Injection Press: The components were molded using a 1200 ton injection press, capable of handling the size and complexity of the grill with impeccable precision.
- Multicolor Class A Painting: To achieve an aesthetically pleasing and durable finish, GPC applied multicolor Class A painting techniques, resulting in a visually striking and resilient product.
- Ultrasonic Welding: The two pieces of the grill were seamlessly joined using ultrasonic welding, ensuring a strong bond and a flawless finish.
- Decal Application: The final touch involved the application of high-quality decals, enhancing the visual appeal of the grill and allowing for customization to meet customer branding needs.
Materials
Color Mated ASA: The project utilized Color Mated ASA, a material chosen for its excellent UV resistance, durability, and ability to be matched to specific colors. This material ensures the grill will maintain its aesthetic appeal and structural integrity over time.
Delivery Timeline
8 Weeks: In a record-breaking 8-week period, GPC completed the tooling and production of the 2-piece plastic grill, demonstrating our rapid turnaround capability without compromising on quality.
Unique Attributes
- Collaborative Part & Welding Design: GPC worked closely with the customer to assist in the design of the part and the welding process, ensuring that the final product met all functional and aesthetic requirements.
- Proprietary “Speedway” Low Volume Tooling Technology: The use of GPC’s exclusive “speedway” technology for low volume tooling enabled the rapid completion of tools, significantly reducing production time while maintaining high standards of quality.
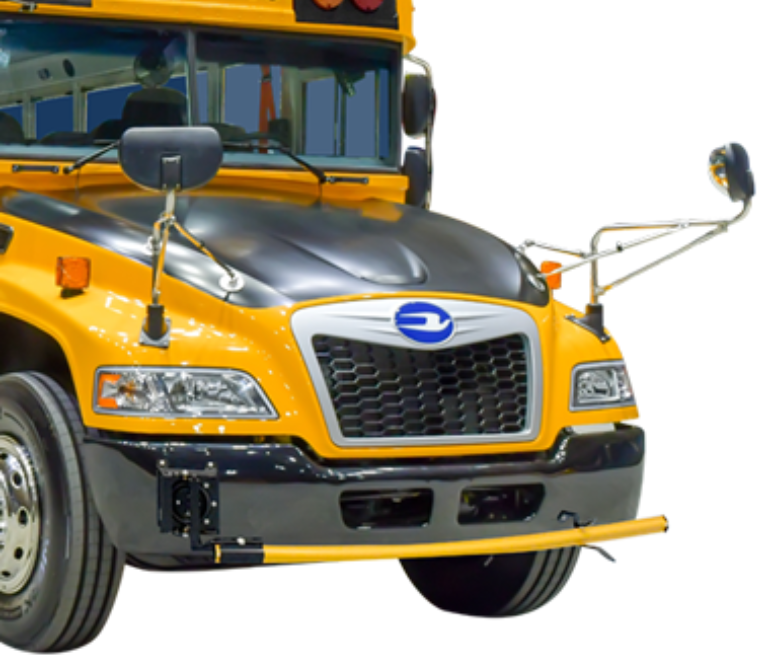
Conclusion
The Low Volume Injection Molding of a 2-Piece Plastic Grill project stands as a testament to General Pattern Company’s commitment to innovation, quality, and customer collaboration. By combining advanced materials, state-of-the-art processes, and a customer-centric approach, GPC has successfully delivered a custom solution that enhances the safety and aesthetics of school buses for Blue Bird Transportation. This project underscores our capability to tackle unique challenges in the transportation industry, providing high-quality, efficient, and tailor-made solutions.